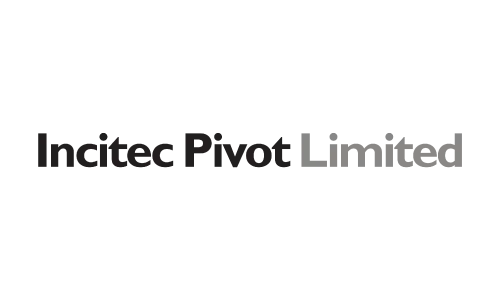
Cataloguing on Demand
Incitec Pivot Limited and Vueterra teamed up to create an on-demand cataloguing service that reduced costs and improved cataloguing delivery and standardisation. Read more…
The Background
Incitec Pivot Limited (IPL) is a global manufacturer of explosives, fertilisers and industrial chemicals. The company has a national inventory of 70,000 stock keeping units (SKUs) within two instances of SAP.
IPL acquired Dyno Nobel in 2008, introducing new explosives production processes and another SAP database to the business. At the time of merger, a review of data and integration of systems was not prioritised and soon, errors and inefficiencies started to emerge across the two businesses due to issues with master data and spare parts catalogues.
Manufacturer part numbers and descriptive information was missing or incorrect. Over time, data quality deteriorated further as users attempted to manually correct issues, inadvertently creating duplicate spare parts records, further error entries and requests in SAP.
At a Glance
SITE:
Incitec Pivot Limited (IPL) is a chemicals, explosives & fertiliser multinational.
ERP:
SAP ECC
PROBLEM:
Spare parts master data issues underpinned poor service levels to internal and external stakeholders, introducing inefficiencies and risk across two IPL companies.
SOLUTION:
Vueterra Inventory & Supply Chain Management Consulting performed:
- Bulk data cleansing & manual data matching to address priority file repair of 20,000 SKUs
- Supplier research and additional entries to the Incitec Pivot SAP environments
- Development of a master data framework encompassing systems and data policies.
RESULTS:
- Consistent data formats, a high-quality spare parts catalogue, accurate inventory and best practice procurement processes across two businesses
- Transaction volume is up, and user effort is down across 6 procurement staff
- Purchase orders processed 55% faster
- Cost savings on outsourced cataloguing: 60%
- On-time delivery of correct operating spares
- A strong foundation is set for continuous improvement initiatives
These master data issues affected almost every process that utilises spare parts information, including:
- Orders couldn’t be completed Procurement teams had poor visibility into existing stock
- Lengthy RFQ processes required constant information from maintenance to sufficiently quote and get to the right end-user
- The manual work required to complete orders generated errors and inefficiencies;
- Incorrect parts were being ordered, manufactured and delivered – an error only identified by the customer once received
- Procurement could not reliably, nor effectively review various suppliers for spare parts, thereby reducing their capacity to competitively source parts according to price and availability.
Without the ability to deliver in-full and on-time, IPL was suffering from major inefficiencies high cost and poor service levels across two businesses and hundreds of staff, including:
- Ordering processes were long, slow and dysfunctional
- Spares ordered by mistake couldn’t be returned, wasting time and money
- Re-ordering parts contributed to longer delivery timeframes and extended equipment downtime, poor maintenance standards and production levels
- Poor visibility into existing stock contributing to inventory management, cash flow and service-level issues
- Employee morale and faith in processes was low due to inefficient, ineffective and unreliable systems
- Poor visibility into existing stock contributed to inventory management, cash flow and service-level issues
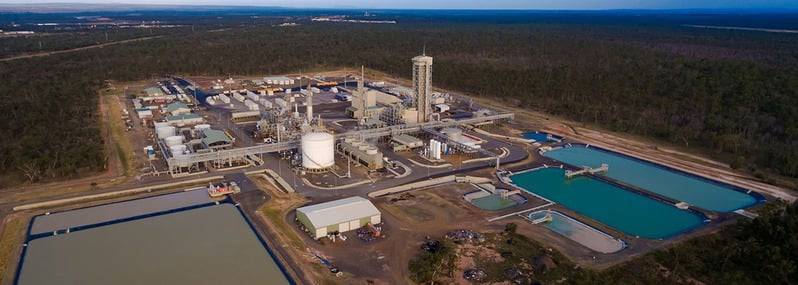
The Solution
IPL originally outsourced their cataloguing to a third party to address the issue related to spare parts, but with-out a view on broader data policies and processes, the service in isolation became expensive and ineffective; IPL’s issues continued.
IPL subsequently selected Vueterra to provide a custom, holistic business solution that would efficiently deliver results right across affected departments.
Vueterra’s specialist knowl- edge of SAP, data governance and procurement best practice won them the job.
The project started with an onsite consultation to review issues, obje-ctives and data across the two businesses; site safety and data cleansing was prioritised. To achieve this: Vueterra’s team analysed and processed the master data to rectify gaps, errors and inconsistencies.
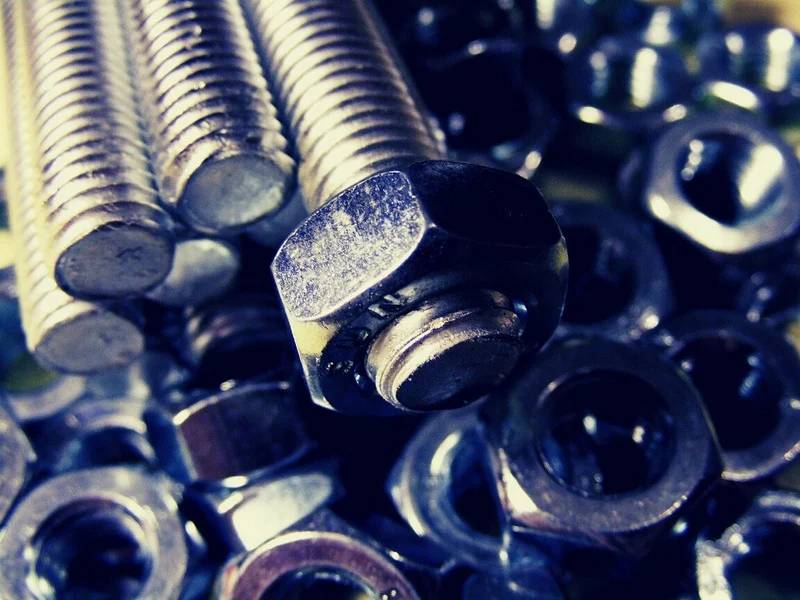
Bulk data cleansing was performed with software and manual fixes where necessary so that information was available to support successful procurement processes.
Vueterra also aligned data and catalogues into a common format so that teams across the two businesses gained visibility of the two SAP databases and their Inventory, providing greater flexibility between the companies.
Once immediate issues were resolved, subsequent items to be undertaken as part of a continuous improvement process were scoped by Vueterrra to help relieve IPL of business pressures and achieve continued maturity. From there, material data and structures were reviewed to optimise parts identification for maintenance teams.
The spare parts data was synchronised with IPL preventative maintenance schedules and equipment strategies that promote site safety. Procurement teams soon gained access to high-quality catalogue data that allowed them to identify the availability and cost of spare parts across multiple suppliers, to drive down supply times and costs. Spend analysis could now take place with greater supplier information which has also led to greater adoption of spares on contracts.
The enablement of contracts has meant higher automation of procurement and closer analysis of supplier lead time performance.Policies and procedures were built to optimise data and supply standards on an ongoing basis according to best practice, and to maintain master data health. This process involved a review of master data, business issues and objectives for a solution to the Master Data issues to be identified, and related processes to be addressed in a continuous improvement process at IPL.
"The spare parts catalogue now facilitates accurate and efficient procurement processes, cutting an average of seven days on previous lead times."
The Results
IPL has achieved uniform, healthy master data and successfully implemented ongoing data policies and processes across separate SAP databases for the fertiliser and explosives businesses.
The spare parts catalogue now facilitates accurate and efficient procurement processes, cutting an average of seven days on previous lead times.
Slashing ordering timeframes by 55 per cent has massive knock-on efficiencies for sales,
maintenance and production teams, and benefited morale between departments across the two entities.
A single version of the truth is available to inventory managers, maintenance and procurement; users can see what stock exists in the other business. Stock levels can be optimised efficiently to balance demand or cash flow.
By addressing data errors and maximising the health and usability of master data through repetitive data governance, IPL was in a position to undertake continuous improvement initiatives, procurement strategy and demand planning to improve service levels, employee and site safety, production levels and competitive sales positions.
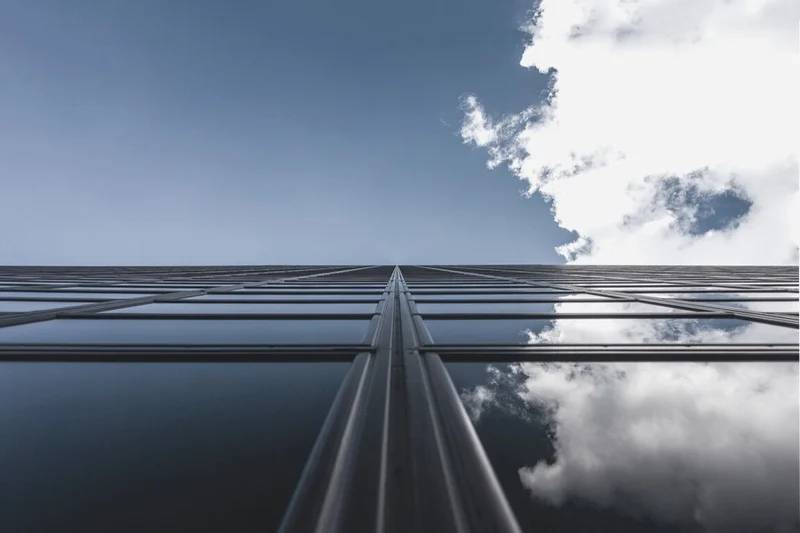
About Vueterra
Vueterra is a specialist in supply chain optimisation with focus on the Heavy, Mining and Government Industries.
Our work is proven to deliver higher service levels and lower costs for clients through solid data governance, procurement best-practice and comprehensive continued improvement programs.
At Vueterra, it’s about getting a view of your business from the ground; gaining insight into the root cause of problems to efficiently address your priority issues, and provide long-term value to the business with custom services built upon our real-world experience.