Throughout your supply chain, there are countless factors that can impact operational efficiency. We take a holistic approach to diagnosing issues in your supply chain, improving data quality and processes along the way. From optimising your inventory management processes to ensuring accurate, real-time data is available for decision-making, we tailor our services to your needs.
Effective supply chain analysis helps you identify gaps, locate opportunities, streamline operations, reduce costs and improve overall performance.
Vueterra prides itself in providing specialist advice and consulting services across the entire lifecycle of the supply chain.
Keeping with our Vue360 philosophy our operational experts have decades of experience across each of their respective functional areas and as a result, are able to tailor solutions to suit your operation’s needs.
By isolating inputs and outputs that cause processes to breakdown and become dysfunctional, we diagnose issues and de-bottleneck your supply chain ensuring that the result means better outcomes for the supply chain customer. As the saying goes, we really want to ensure every “cog in the wheel” is well oiled and functioning smoothly.
Our Supply Chain Health Check is designed specifically to optimise your supply chain and deliver a step-change improvement that leads to better value for the supply chain customer.
01. MASTER DATA
Quality, accurate and reliable master data is without a doubt one of the most crucial components when it comes to developing a mature supply chain which operates smoothly and efficiently.
The notion of “Do It Right The First Time” definitely applies to this function, however despite the large majority of organizations having good intentions and aspiring to do things properly from the start, we still come across a proportion who require assistance either in fixing legacy issues (e.g. post-ERP migration) or in enriching the overall quality of their master data and improving their master data governance frameworks.
Vueterra’s team are able to assess the maturity of your master data across a range of metrics including but not limited to;
- Cataloguing processes
- Approval Workflows
- Taxonomies & Data Dictionaries
- Description Framework
- Material Group Framework
- Cataloguing processes
- Approval Workflows
- Taxonomies & Data Dictionaries
- Description Framework
- Material Group Framework
By assessing the current state of your master data against our criteria of what is considered best practice. We can quickly identify areas of immediate improvement and recommend suitable improvement strategies and project management timelines for short- and long-term engagements.
Ultimately, we believe the simplest things an organization can do to improve their supply chain are to;
- Embed Description and Material Group Frameworks to make finding and ordering parts easy and seamless
- Leverage the power of your ERP to manage part supersessions and avoid duplications
- Develop exception reporting to quickly identify and rectify areas of misalignment
02. INVENTORY
Once you have your master data setup correctly, how do you maximise the efficiency of your Inventory and strike the right balance between optimising working capital v/s ensuring a high level of parts availability?
Holding inventory is about more than just a simple Reorder Point formula involving Lead time consumption and Safety Stock – it’s about putting in place policies and procedures geared towards delivering the right material to the right place and at the right time, as safely and as efficiently as possible.
In order to meet all of those requirements there are a number of key processes which we at Vueterra can review and implement across both the Inventory Analytics and Inventory Planning streams.
Inventory Analysis
Inventory Analysis relates to all things working capital optimisation. We call this optimisation as the focus should be on holding the “correct” amount of stock as opposed to “less” or “surplus” stock.
There are a few critical enablers to standing up an effective inventory analysis function, namely;
- A clearly-defined Inventory Segmentation policy (insurance spares, capital spares, critical spares, obsolete stock, fast-moving stock etc)
- An approval framework for reviewing and applying changes to inventory settings (involving both Supply and Maintenance leadership teams)
- An inventory optimisation software which takes the above rules, applies them to your inventory dataset and produces a list of recommendations around Min/Max levels
- Standard Operating Procedures and Checklists which detail the daily, weekly and monthly tasks associated with actioning recommendations from the software
- Reporting Dashboards to track the completion and impacts of tasks and where continuous improvement or management is needed.
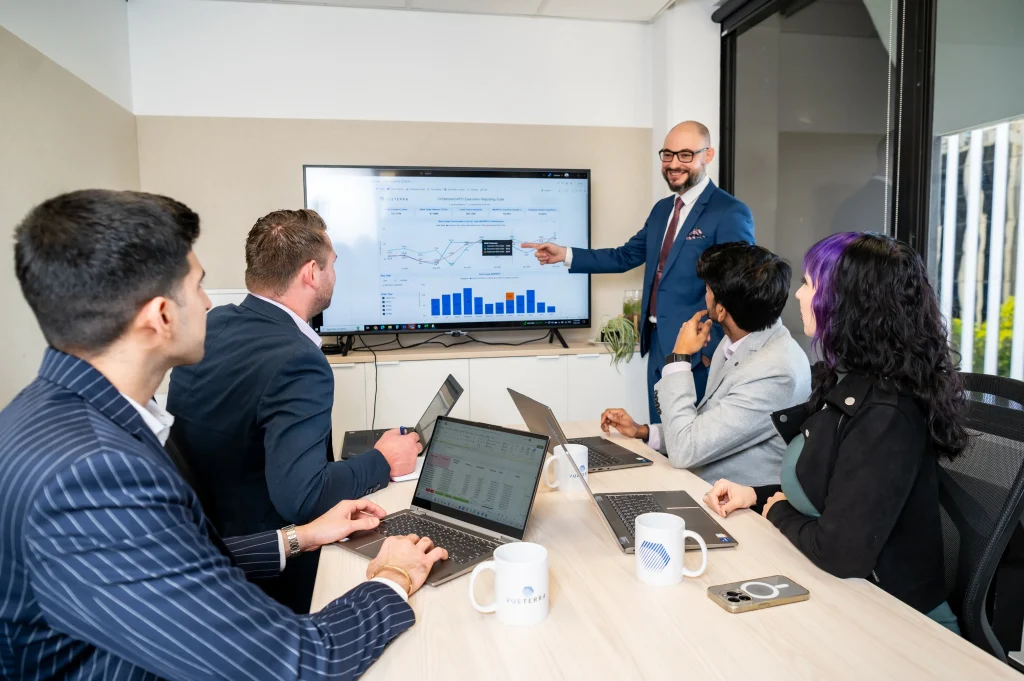
Inventory Planning
Once inventory settings have been optimized, the Inventory Planning function is charged with ensuring settings are operating as expected and servicing maintenance demand.
Inventory Planners monitor incoming demand and take corrective action to ensure there is sufficient material to meet demand, be it by expediting a purchase order or rescheduling demand to a future date.
The Inventory Planning function also acts as an interface between Maintenance, Warehousing and Purchasing, as well as the Inventory Analysis function. In some organisations the analysis and planning roles can be performed by the same person.
Core to the Inventory Planning role is the coordination of information between the aforementioned parties, this can take several forms;
- Attending regular scheduling meetings with maintenance planners to gain alignment on upcoming materials required for both planned and shutdown work
- Providing reporting on parts availability for upcoming work
- Liaising with the Purchasing team to expedite orders and/or organise express freight
- Liaising with the Category Management team to ensure long term demand forecasts are being taken into account with regards to relevant contract negotiations
- Relaying any updates or changes required to material settings to the Inventory Analysis team
The Vueterra team have extensive experience rolling out inventory stabilisation projects which address all the above enablers – we can quickly assist you in getting your operation into ship-shape so that your team members can be more effective in their daily work and are focusing on the right things.
03. CATEGORY MANAGEMENT
Once your master data is aligned and your inventory settings and procedures are optimised, how can you rely on the information in the system to support the logic which goes into calculating Min/Max levels? What if your levels are based on an agreed contracted lead time of 60 days, yet the vendor consistently fails to meet that target and delivers on average every 90 days?
Without proper alignment and support further up the supply chain then inventory levels are meaningless – this is where robust Supplier Relationship Management and Contract Management practices are necessary to ensure reliability in the supply chain.
Some of the processes Vueterra can help establish include;
- Contract tendering and awarding framework
- Review or installation of an appropriate Contract Management system
- Review of supplier master data
- Spend & Approval frameworks
- Contract Management frameworks and Reporting
The Contract Management framework in particular is key to ensuring suppliers are delivering in full and on-time, it is a minimum requirement to ensuring the smooth functioning of your supply chain.
04. PROCUREMENT
You have stabilized your inventory settings and you have embedded processes for managing suppliers, how do you then equip your Procurement Team to work effectively within those frameworks?
Once contracts and purchasing agreements are in place, there is a need to ensure the processes and procedures of the Procurement team are robust enough to ensure conformance with a range of supplier performance metrics.
For the most part, this involves the development of extensive reporting to track the following;
- Purchase Order automation
- Purchase Order conversion time (for manually created Purchase Orders)
- Requisition approval times
- Outstanding / Aged Purchase Orders
- Delivery in Full and On Time (DIFOT)
05. WAREHOUSING
The warehouse is an often over-looked area when it comes to supply chain optimisation, yet it plays just as important a role as Master Data. Having a mature and efficient warehouse management framework reduces noise further up the supply chain and more importantly provides maintenance teams with more confidence in the supply team’s ability to meet their requirements.
Warehouse Management extends beyond simply receiving/despatching materials and conducting stocktakes, the warehouse team is a true “team” in the sense that each and every team member has a specific role that forms part of an overall Roster of daily, weekly and monthly activities.
Vueterra can assist with conducting an extensive warehouse management review by assessing the maturity of your operation across each of the following areas;
- Overall warehouse process maturity
- Policies and procedures around receipting, despatch, stocktakes, returns and disposals
- Quality Control processes (QA, QC and quarantine)
- Safety & Materials Handling policies (particularly around spares preservation)
- Reporting around Roster activities & Service Level Agreements
The warehouse is truly the “face” of the supply team at a site level and as such can be on the receiving end of a large number of queries across the operation. It is important to develop processes that empower the team to focus on their core tasks, as opposed to putting out fires due to inefficient processes across other supply chain functions.